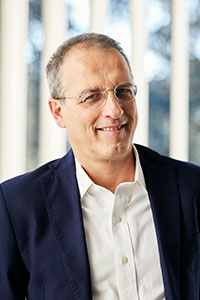
by Antonio Mosca,
Head of Digital Transformation, Fabio Perini S.p.A.
Since the 2009 recession, the Tissue sector has been growing between 3%-4% per year, mainly thanks to China. A benchmark of the Top 12 global tissue players‘ results, based on financial year 2018 annual reports, shows the worst results since 2013, with average EBIT margin dropped from 16.0% in 2017 to 12.5% in 2018.
Four companies reported a negative EBIT and none of them improved results in 2018 compared to 2017. On top of this, in 2018 the tissue industry suffered from high pulp prices, which affected margins a lot, since pulp accounts for more than two thirds of manufacturing costs of jumbo reels.
In this context, OEE concerns start. Let’s see why: beginning of 2019, a survey made by StepChange Consulting among managers, decision makers and stakeholders from the European pulp, paper, tissue and packaging industries showed Industry 4.0 digitalization as the top trend, ranked at 75% among all the respondents. Guess what? Asking participants from the tissue industry about their expectations regarding the highest benefits from digitalization/Industry 4.0 for their businesses, 78% named cost reduction: here OEE increase plays an important role.
High OEE as a Competitive Advantage
Very simple: who is able to cut inefficiencies will recover profitability. In other words, the higher the OEE the higher the EBIT.
Digital solutions are enablers for OEE increase: the potential impact on OEE due to digitalization is above 50%, according to various studies. E.g. Stepchange Consulting estimates for the Tissue market:
· Up to 50% in reducing the downtime
· 5-10% in increasing productivity
· 10-30% in maintenance cost reduction
Another study by McKinsey, specific for the Paper market (that includes Tissue) estimates a potential 5% OEE improvement with existing technologies that becomes 15% including future technologies.
Potential Benefits
Measures done on some Tissue Customers show that 1 point per cent of OEE increase equals to around 4000€ impact on profit per month. In a pilot project aiming at optimize machines performances via a digitally-enabled process parameter AI-driven optimization, the result was up to 10% of output increase. With other Customers, when digital and humans’ capabilities are mixed together the increase may rise up to 30-40%. That’s precisely the concept behind our Digital Tissue and Tissue Performance Center propositions.
A Mix of Digital Technologies and Humans’ Know-how
In order to increase OEE, we have adopted a two-fold approach:
At first, we have started developing smart machines and smart lines. That means converting and packaging machines that allow downtime reduction, high quality standards and diversified production. An example above all is coming from “Constellation™”, a cutting-edge converting rewinder that grants high quality standards even with higher speeds, enables to eliminate critical regulations and allows more stability independently from the paper and the embossing variations.
Besides the machines, we are also busy proposing to our Customers specific TIPs (Technical Improvement Programs), aimed to address specific topics and contribute to increase the OEE. The “Automatic Blade Change” and the “Easy Reel Change” are some of the latest examples of the Technical Improvement Programs that enable downtime reduction (90% average time reduction for blade replacement; average of 90 seconds to change the paper reel) and safety increase.
The second dimension is to make our Customers’ factories smarter, for example by empowering their operators when performing operations and maintenance activities. In this case we have developed a number of smart applications, better known as Digital Tissue™, able to support operators monitor converting and packaging processes to streamline operations and maintenance autonomously or, if needed, to establish a remote connection to enable our experts to provide on-line support.
Furthermore, with the launch of our Tissue Performance Center, we have raised the bar of support we can provide to our Customers. The Tissue Performance Center is a next generation technologic environment where expert engineers, supported by data scientists, continuously register and analyze customers’ data to supply information on the machines status and suggest improvements to maximize the OEE of the production lines. Thanks to the direct connection with the customers’ machines, the Tissue Performance Center can now work proactively, not just reactively, as it used to in the past.
An Outlook on Future
At Fabio Perini we want to position ourselves as a reliable partner to help our Customers in keeping OEE at the optimal level. This implies to continue to design and build even smarter machines, and develop digital capabilities to make our Customers’ Operations & Maintenance activities smarter.
Please note that “Optimal OEE” not necessarily means the highest OEE! In fact, the major enemy of indiscriminate OEE increase is over-capacity: as an example, in Western Europe we expect +400KTons capacity against an expected +150KTons of consumption growth. So the business point is: under which circumstances a Tissue producer really need an OEE increase? To be able to identify such circumstances is the best way to approach Customers. That’s why we have developed a tool to predict production trends in the Tissue market based upon actual data collected by our Customers’ lines.